As part of our Quality Control process we periodically check production forks against the same ISO 4210-6 test standards that we use during the R&D behind each part or product.
The process covers both fatigue and impact testing and is very noisy.
Fatigue testing involves the application of force with rapid repetition perpendicular to a fork’s axle, to simulate a lifetime’s worth of washboard roads and uneven pavement. Impact testing is meant to show the result of a sudden application of a singular force — like an impact with a curb or a car in the real world — with the goal of preventing a catastrophic failure that would leave the fork completely broken.
The sweet spot is of course in having both the resilience to live a long life in the face of relentless road chatter and a stout construction that, in the case of a sudden and very hard hit, will absorb energy and remain intact to function as designed until a controlled stop can be made.
Our forks are tested on the Oregon Bicycle Constructors Association Fork Smasher (official title) and take several hours to complete. Watching the machine run one can’t help but nerd out, and watching the cycle counter roll up to and over 100,000 repetitions during the fatigue test is pretty satisfying.
Did we mention it is noisy?
It is also satisfying, in a far more giddy way, to take a fork that has already gone through the 100k cycles of the fatigue test and watch it pass the rearward impact test. The impact is violent and can easily destroy any under-built fork of any material. (There are different test regimens for suspension and rigid forks, but no distinction in criteria based on materials).
We recently pulled one of our TiGV titanium production forks from our regular QC process to run through the full battery of abuse from the Fork Smasher. This particular fork had been tagged for a couple of cosmetic issues that were extremely mild by most standards but were enough to tickle our OCD, and we were curious to find out if they would have any functional effects.
Reminder: The machine makes a lot of noise!
After completing both test cycles we pulled the fork off of the machine and gave it an inspection. We were pleased to see that the design had functioned perfectly, taking the marathon pounding of the fatigue test like a champ and then absorbing the force of the impact test squarely and without catastrophic failure. The gentle fold deformation at the point where the fork leg curves into the tapered crown is the only resulting damage, and is the exact failure mode we would want to see a rearward impact situation — less than 45mm of permanent deflection with the axle/fork legs remaining perpendicular to the bicycle centerline.
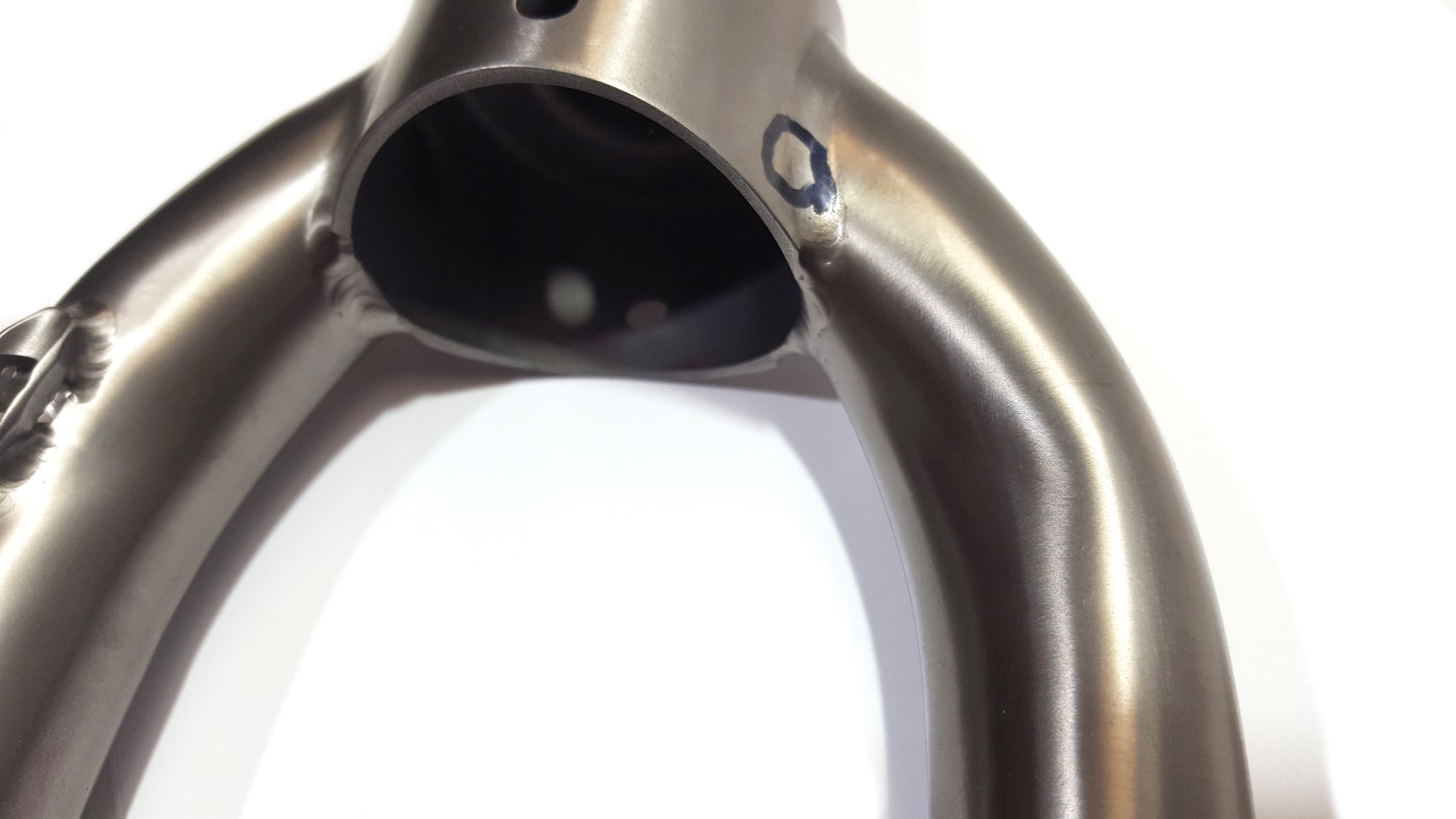
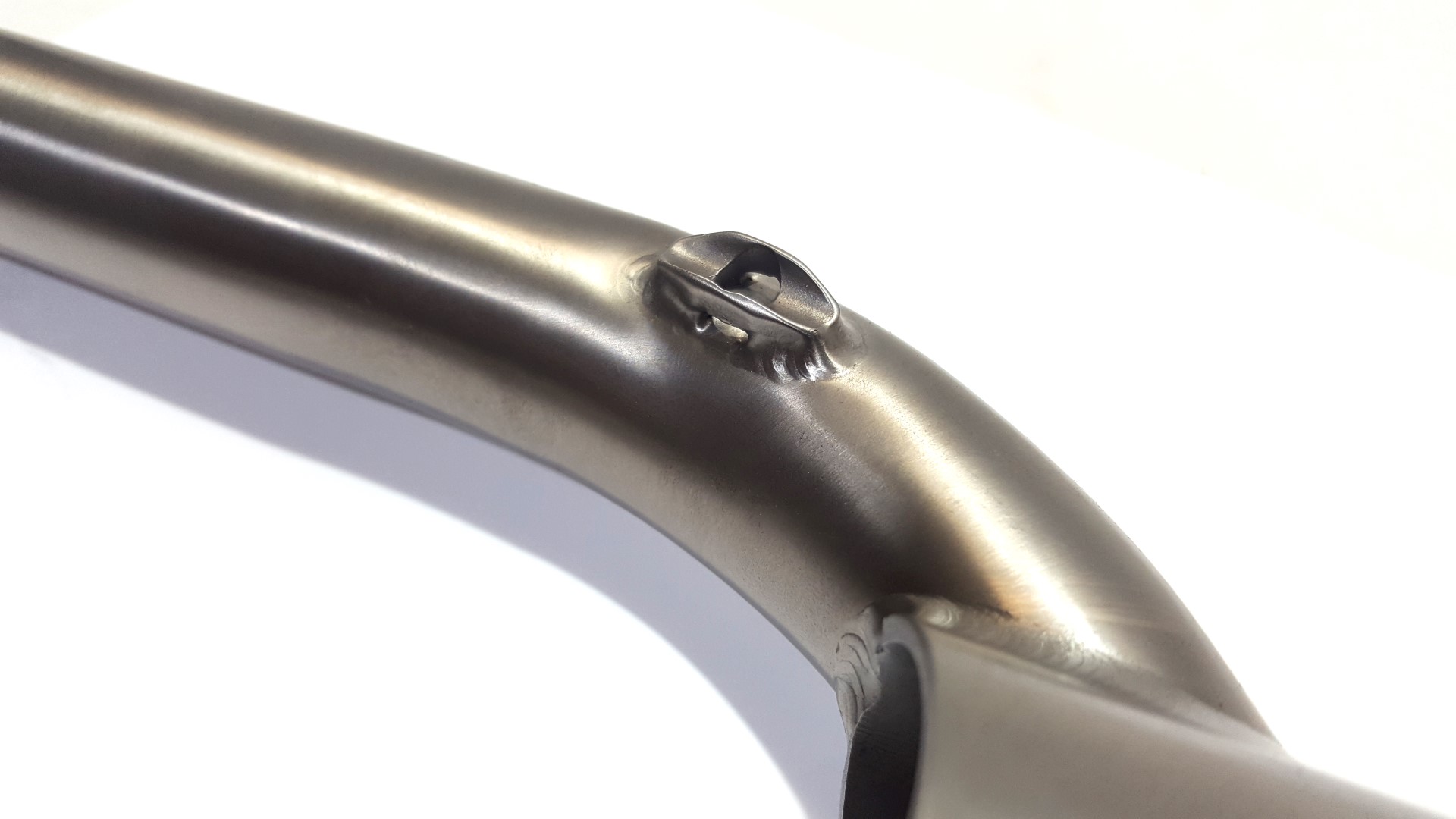
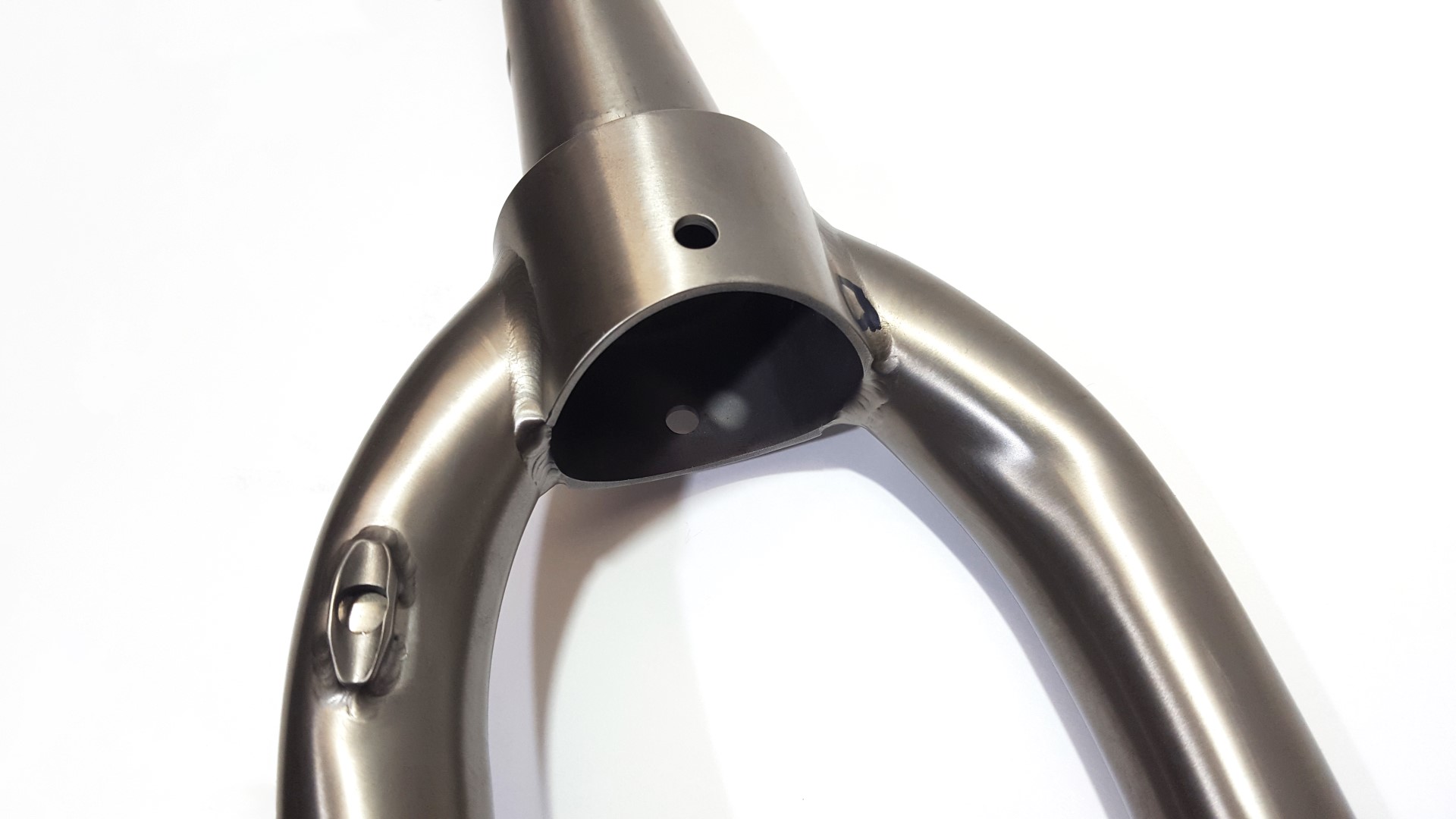
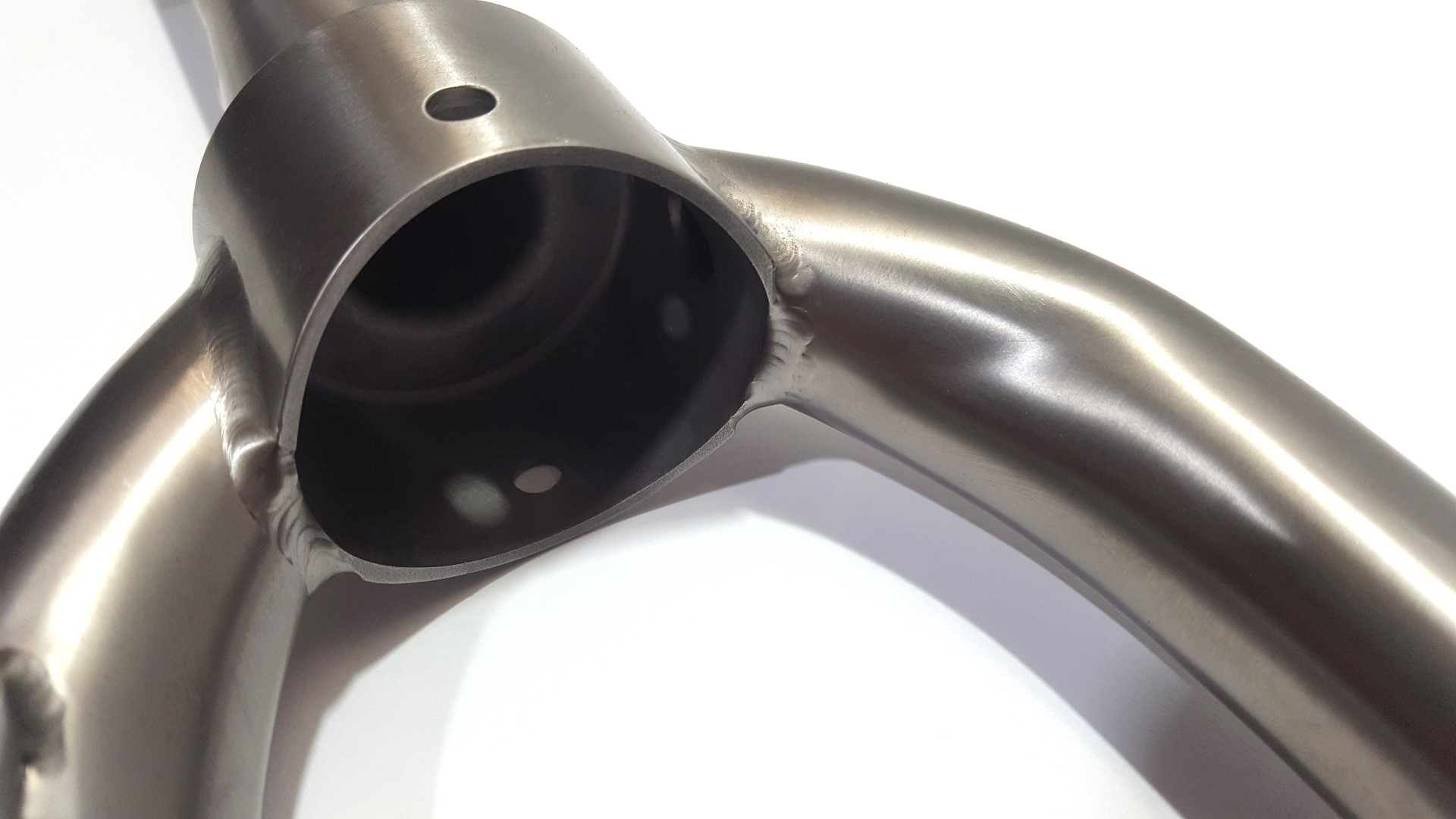
We'll maybe invent some new torture tests and keep beating on this until it breaks... or doesn't. When prototyping our 1.5” tapered titanium steerer a few years ago we eventually got tired of the noise and turned the machine off after a second 100k+ cycles. 🙉